ساییدگى تیغه راکل در چاپ گود (هلیوگراور)
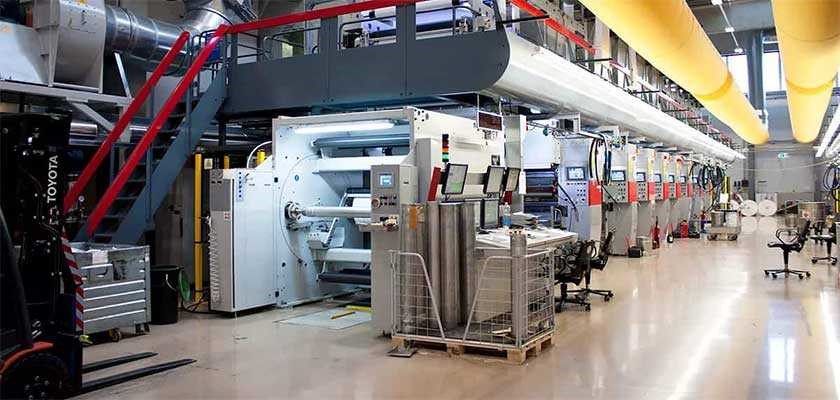
فرسودگى تصادفى تیغه راکل، ناشى از دانه هاى خراش دهنده و ساینده ها است که تولید خراشیدگى مى کنند. وقتى با ناخن روى تیغه راکل را امتحان کنیم پستى و بلندى ها و قوس هاى کوچکى احساس مى کنیم. براى این که تیغه راکل به حالت اول باز گردد، باید با کاغذ سمباده ظریف آن را بساییم تا پستى و بلندى ها از بین برود.
تیغه راکل نو تیغه راکلى است که منتهى الیه آن تراشیده شده باشد. فعالیت و تمیزکارى چنین کاردکى خیلى مؤثر و مفید است. به قسمتى که ممکن است بر سیلندر نو آسیب برساند و تیغه هاى ترام کنده شود. بنابراین لازم است آن را قبل از به کاربردن با سنگ سمباده یا کاغذ سمباده بسایند تا گوشه نوک آن گرد شود. تیغه راکل مستعمل و فرسوده در تمیزکارى ضعیف عمل مى کند. یک گراور سبک (کم ارزش) مستلزم وجود تیغه راکل مستعمل و فرسوده است و گراور سنگین مستلزم تیغه راکل نو مى باشد.
فرسودگى عادى تیغه راکل با ساییدگى کاغذ، فویل و مرکب و زمان چاپ هر سیلندر رابطه مستقیم دارد. تیغه راکل ها را در رأس مدتى که برحسب عوامل مختلف متغیر است، تعویض مى کنند (عمر مفید).
اپراتور مراقب، با آزمایش فویل یا کاغذ چاپ شده، تعیین مى کند که آیا تیغه فرسوده شده است یا نه. ممکن است تیغه راکل پس از چاپ ۵۰۰ یا پنج هزار دور سیلندر فرسوده شود کما اینکه ممکن است پس از چاپ ۴۰ هزار یا ۴۰۰ هزار دور سیلندر فرسوده شود. اینجا کیفیت تشخیص و ارزیابى و همچنین عادات و نحوه عمل اپراتورها اهمیت دارد تا به محض اینکه در تیغه راکل آثار و علائم فرسودگى مشاهده کنند آن را تعویض مى کنند. البته برخى هم آن را با سنگ سمباده ساییده و نتیجتاً فشار تمیزکارى را اصلاح مى کنند.
تیزکردن تیغه راکل (دکتر بلید): تیز کردن تیغه با دست و با یک سنگ دستى انجام مى گیرد. سنگ زدن را با یک خط کش یا صفحه صیقلى آزمایش مى کنیم که سطح تیغه یکنواخت شده باشد. در نتیجه وقتى تیغه راکل را بر روى سیلندر قرار مى دهیم سطح مرکب را به طور یکنواخت پاک خواهد کرد. اولین بارى که تیغه را تیز کردند، با سنگ سمباده نوک آن را گرد مى کنند. تیزکارى با ماشین مستلزم احتیاط فراوانى است تا فلز نسوزد و پوسته نکند. براى جلوگیرى از این امر باید موقع تیز کردن مراقب بود که فلز مرتباً خنک شود، در غیر این صورت بر اثر محکم کشیدن سنگ تیزکن، حرارت شدید تولید شده و فلز را پوسته پوسته مى کند.
اپراتور ماشین باید همه روزه و یا گاه به گاه با سنگ سمباده بر روى تیغه بکشد تا ساییدگى آن از بین برود. در ماشین چاپ رنگى هم عیناً همین روش را در مورد تیز کردن تیغه باید به کار برد.
شرایط خوب کارکردن تیغه راکل
۱. لبه تیغه که بر روى سیلندر قرار مى گیرد همیشه خوب تیز باشد و ناهموارى و بریدگى نداشته باشد.
۲ . سطح سیلندر چاپ سالم باشد و به طورکلى حالت لنگى نداشته باشد.
۳. در طول کار بین سیلندر و تیغه، ناخالصى پیدا نشود و فقط مرکب بین تیغه و سیلندر وجود داشته باشد.
۴. تیغه خوب، پهن بوده و از نظر مکانیکى میزان شده باشد.
عوامل زیر در انتخاب تیغ مناسب موثر می باشد:
ضخامت تیغه
فاصله تیغه با پشت تیغه
خمیدگى روى سیلندر چاپ
فشار در حدى که سطح اضافى مرکب را از روى سیلندر بردارد.
میزان بودن حرکت جانبى
سختى و صلابت فولاد تیغ نسبت به سختى و صلابت کُرم سیلندر.
دمیدن روى سیلندر
هرگاه تیغه مستعمل و یا فرسوده، و یا سیلندر خراش برداشته باشد، روى ورقه چاپ شده، رنگى به چشم مى خورد که به علّت باقى ماندن مرکب اضافى در سطح سیلندر است. براى جلوگیرى از این امر بین تیغه و سطح چاپ، یک دستگاه دم که هوا را روى سیلندر مى فرستد و مرکب باقى مانده روى سطح سیلندر را خشک مى کند، نصب مى شود. دمیدن هوا همچنین وسیله اصلاح گراور خیلى قوى در رنگ هاى روشن است و روى تمام یا قسمتى از طول سیلندر نصب مى شود.
سیلندر فشار(رول پرس)
فشار به وسیله سیلندر بر روى فویل و یا کاغذ که از بین سیلندر چاپ مى گذرد و به وسیله سیلندر فشار مرکب که از گودى هاى سیلندر منتقل مى شود، بلافاصله در مسیر خشک کننده قرار مى گیرد. عمل خشک شدن چاپ طورى در ماشین پیش بینى شده است که رنگ اول پس از آنکه از سیلندر به وسیله سیلندر فشار بر روى فویل قرار گرفت، در طول مسیرى که باد گرم در آن جریان دارد خشک شود. به وسیله یک غلطک کائوچویی که حالت ارتجاعى آن ۷۰ الى ۷۲ مى باشد براى ماشین هاى چاپ تعیین مى گردد.
سیلندر فشاردهنده (سیلندر رول پرس): سیلندرهاى فشاردهنده هیچ گونه پوشش موضعى ایجاد نمى کنند. کیفیت چاپ روى سیلندرها به خوبى احساس مى شود. مکانیسم فشار ممکن است از یک یا دو سیلندر تشکیل شده باشد، یا خود فشاردهنده مجهز به کائوچو، به اندازه کافى سنگین بوده و به سیلندر چاپى تکیه داده شود و یا نقش آن به طور ساده، ارتجاعى بوده و یک سیلندر دوم از جنس چدن یا فولاد نیز به آن ضمیمه شود. در هر دو مورد فشاردهنده با سرعت زیاد، هماهنگ با سرعت ماشین، بدون آنکه فرمانى به آن داده شده باشد مى چرخد. در ماشین هاى مدرن که در حال حاضر ساخته مى شود، فشار سیلندر پنوماتیک و یا هیدروپنوماتیک مى باشد. عدم امکان تغییرات موضعى پوشش و بى نظمى هایى جزئى در فشار روى ماشین هایى با قطر بزرگ و بى نظمى هاى احتمالى سیلندر یا فشار دهنده و مخصوصاً اختلافات نرمى کاغذهاى مختلف چاپ، ثابت مى کند که فشاردهنده حتماً باید به کائوچو مجهز باشد تا خاصیت ارتجاعى پیدا کند.
تماس فشاردهنده و کاغذ و سیلندر بر طبق یک خط هندسى انجام نمى گیرد، بلکه بر طبق نوارى با عرض متغیر، به تناسب ارتجاعى بودن کائوچو، صورت مى گیرد که حدّ متوسط آن ۱۲ میلى متر است. فشاردهنده نرم به کاغذ امکان مى دهد که از حفره هاى سیلندر، بهتر مرکب بگیرد؛ لیکن بر اثر لغزش ذرات کائوچو برروى یکدیگر فشاردهنده گرم شده و کائوچوى نرم آن، به خصوص در هنگام سرعت زیاد، زودتر فرسوده مى شود.
همچنین، هرگاه فشاردهنده با کاغذ خراش دهنده یا ساینده اى که در آن ذرات معدنى در سطح کاغذ باقى مانده باشد، کار بکند به سرعت خراب مى شود.
روى ماشین هایى با عرض زیاد، باید فشاردهنده هاى خیلى سخت به کار برد تا تغییر شکل ندهند. روى همه ماشین ها، کائوچوى فشاردهنده باید طورى باشد که کاملا به استوانه فولادى بچسبد و در برابر فشارهاى تاب خوردگى مقاومت کنند.
مسئله اى که کیفیت فشار به وجود مى آورد این است که اپراتور را عملاً مجبور مى کند که بین کیفیت فشاردهنده ها سازش و هماهنگى به وجود آورد. راه حلى که در این زمینه وجود دارد این است که براى هر ماشین چند دستگاه فشاردهنده با استانداردهاى مختلف داشته باشیم و از بین آنها آنکه بهتر به کاغذ و فویل ها سازش دارد را انتخاب کنیم.
فرسودگى فشاردهنده تابع سرعت دورانى آن ها مى باشد.
هرچه قطر آنها بیشتر باشد، کمتر گرم مى کند. بنابراین به نفع کاربر چاپ است که براى ماشین هاى سریع، فشاردهنده هایى با قطر زیاد به کار ببرد. لیکن از طرف دیگر فشاردهنده هاى بزرگ، سنگین تر بوده و حمل و جابه جا کردن آن ها مشکل است.
سختى و سفتى فشاردهنده به مرور زمان و به تدریج که از قطر آن کاسته مى شود افزایش مى یابد. حد نصاب این افزایش ۳ درجه (شور) مى باشد ولى حد نصاب قطر نباید از۰/۵+ درجه میلیمتر تجاوز نماید.
میزان کردن فشار
میزان کردن و تنظیم فشار از تغییر نیرویى که به فشاردهنده وارد مى آید حاصل مى گردد. دستگاه هاى جدید فشار بادى کنترل تعادل حرکت و فشار را امکان پذیر ساخته است. فشار لازم براى چاپ بستگى به نوع فویل ۲ و یا کاغذ دارد به همین دلیل کاربر چاپ غالبا مجبور است که نوع فشار را طورى تنظیم کند که نقش روى سیلندر به فویل و یا کاغذ منتقل شود.
استحکام و سختى فشاردهنده بستگى به موارد زیر دارد:
براى سلفون و پلاستیک : فشار ۵ کیلوگرم و سختى فشاردهنده ۶۰ درجه است.
براى کاغذ قشردار : فشار ۱۵ تا ۲۰ کیلوگرم و سختى فشاردهنده ۷۰ درجه است.
براى کاغذ سخت و مقوا : فشار ۲۲ تا ۳۷ کیلوگرم و سختى فشاردهنده ۸۵ درجه است که براى مقواى سخت ۹۰ درجه مى باشد.
میزان کردن فشار در منتهى الیه فشاردهنده صورت مى گیرد. نیروى فشار ارتجاعى است. فشار هوا از طریق فنر تحت فشار به وسیله فرود آوردن بالشتک هاى فشاردهنده و غلطک متکى به آن صورت مى گیرد و یا به وسیله دوران گریز از مرکز با دست یا موتور برقى انجام مى گیرد.
زمانى که ماشین متوقف شود، فشار دهنده ها را چند میلى متر با دست و یا به وسیله سیستم برقى بالا نگه مى دارند تا کاغذ به سیلندر نچسبد.
فن هاى خشک کننده مرکب
دستگاه هاى خشک کننده
دستگاه هاى خشک کننده بسیار گوناگون اند و ساختمان آن ها عموما متفاوت است. مدل هاى جدید داراى یک گیرنده مواد فرّار تبخیر شده هستند و از یک محفظه بسیار محکم تشکیل شده اند که در آن فویل بطور مداوم عبور می کند. هوای معمولی در این محفظه دمیده می شود. مخلوط هوا و حلال فرار به درون محفظه مکیده شده و به خارج کارگاه هدایت می شود.
مؤثر بودن در خشک کردن بستگى به درجه فرار بودن و مقدار هوایى دارد که فویل با آن در تماس است و نیز بستگى به کیفیت این هوا از نقطه نظر خشک کردن دارد. درجه تأثیر آن تابع سرعت نسبى جسمى است که با آن در تماس است (یعنى هوا و فویل) زمان خشک کردن بر اثر سرعت هوا خیلى سریع و تقریباً با این عمل هوادهى متناسب است. حتى اگر اختلاف درجه حرارت ثابت باشد.
براى صرفه جویی در خشک کردن، باید تعادل بین حرارت و سرعت به دست آید. هر چه بخار فرّار، محیط کار سریع تر برداشته شود، عمل خشک کردن بهتر صورت مى گیرد (توضیح اینکه دستگاه هاى خشک کننده مرکب هم در چاپ فلکسو و هم چاپ روتوگراور یکسان مى باشند).
خشک کردن مرکب
بعد از آنکه به وسیله سیلندر فشار، نقش از روى سیلندر به فویل منتقل شد، از کانال هاى فن و باد گرم عبور مى کند. هوا به وسیله عبور از لوله هاى بخار یا مقاومت هاى الکتریکى گرم شده و به وسیله یک فن هواى گرم دمیده مى شود. درجه حرارت به سهولت قابل میزان کردن است. فویل در دومین محلى که در ادامه محل خشک کردن است دوباره سرد مى شود. هوا از منافذ محفظه اى که فویل را احاطه کرده دمیده مى شود. در حین خروج، بخارات فرار بوده و از منافذ دیگرى خارج و سپس از یک لوله خروجى از کارگاه خارج مى شود.
منبع: چاپخونه